得意先の要望で「計量器プリンタ」という機器を作っています。
言わば裏メニューのような商品で大きく宣伝はしていない商品です。
主に外国製の電子精密計量器(電子天秤)に接続(RS232C通信)して、 計量された値をプリントアウトする機器です。
メーカオプションでプリンタのライナップがあるのに何故弊社が作っているかと言いますと、 メーカのオプション品は計量物の値をプリントするか、風袋を計量して、 その後に計量物を足した値をプリントするものが一般的のようです。
風袋に計量物が入っている場合や風袋をタイラップのようなもので束ねている場合など、 その工程が別工程の場合、
【 (風袋+計量物)-風袋 】としないと計量物の値が算出されません。
弊社のプリンタはテンキーが付いていて、例えば、あらかじめ計量してあった風袋を引いた値をプリントすることが出来ます。
風袋がいくつかある場合その風袋もプリントすることも出来ます。
値を引くという概念が、既製品にはなかったのだと推測します。
弊社ではユーザーの要望に合わせたカスタマイズにも対応しています。
昨年の秋に、新型機(mpr45a/b)の製造を開始しました。
現在まで10台程度出荷させていただいています。
旧型機(MZB-27)も100台ほどが出荷されている商品です。
通信設定がわかれば国内、国外の計量器に対応することは可能です。
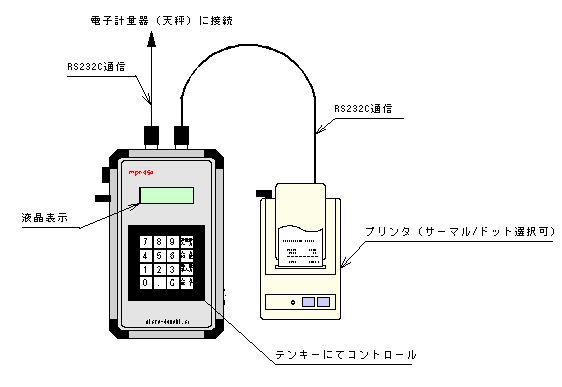
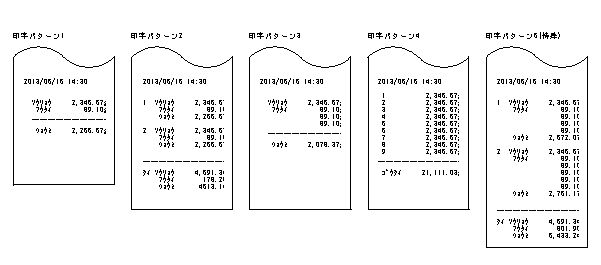
今までは裏メニューでしたが、 便利だと思っていただけるユーザー様があれば、ご利用いただければと思っています。